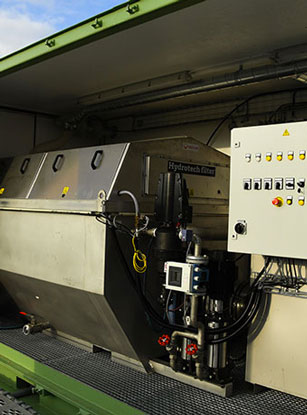
Enhanced C extraction
Municipal wastewater contains a variety of organic substances, and the embodied carbon represents a potential source of chemical energy. Traditional WWTPs separate a fraction of this carbon (up to 50%) into primary and excess sludge, while the remaining part is converted to CO2 in biological treatment by microbial biomass. The latter part requires a high amount of electricity for oxygen supply, and wastes the potential energy contained in this part of the organic matter.
Enhancing the extraction of carbon into sewage sludge in the WWTP process will increase the potential biogas yield and decrease efforts for treatment, thus improving the overall energy profile of the WWTP considerably. Enhanced carbon extraction can be realised by advanced primary treatment combining chemical dosing with sedimentation, filtration or flotation processes to separate most of the particulate matter. After enhanced carbon extraction for energy recovery, downstream biological nitrogen removal has to be optimised to safely fulfil effluent quality targets.
-
What purposes?
-
Which technologies?
-
Where?
Technologies
Chemically enhanced primary treatment
The primary treatment stage in a WWTP usually consists of a sedimentation tank or settler, where particulate matter is separated from influent wastewater by simple gravity-driven sedimentation. Due to their high specific weight, particles settle to the ground and are collected there as primary sludge, normally operating at retention times of 0.5 to 2 hours. To enhance the separation of smaller particles and reduce required retention times, coagulation and/or flocculation can be added upstream of the settler, which is then called chemically enhanced primary treatment (CEPT). Dosing of metal salts and/or polymer aggregates smaller particles and colloidal matter into larger aggregates, which can then be separated by gravity.
Chemical dosing can be combined with lamellar settlers which provide a high surface area for settling and thus allow a more compact design. The combination of coagulation and/or flocculation tanks and lamella settler can also be enhanced with sand as a nucleation agent of flocs, which is then called “ballasted sedimentation”. The sand is separated from primary sludge by hydrocyclone before being recycled to the flocculation tank. CEPT allows a higher extraction of COD in primary treatment (up to 50-70%) than simple settlers and thus can be a first step for an energy-efficient WWTP scheme.
- Paper on CEPT
- Discussion of CEPT
- An Introduction to Chemically Enhanced Primary Treatment
- Report on options for primary treatment
-
Purpose
-
Approach
-
Where?
Dissolved air flotation
Dissolved air flotation (DAF) is a water treatment process that clarifies wastewater by the removal of suspended matter such as oil or solids. The removal is achieved by dissolving air in the wastewater under pressure and then releasing the air at atmospheric pressure in a flotation tank basin. The released air forms tiny bubbles which adhere to the suspended matter causing the suspended matter to float to the surface of the water where it can then be removed by a skimming device. DAF can be operated with upstream dosing of coagulants or flocculants to agglomerate particulate matter and enhance elimination efficiency.
The process can also be combined with lamellar settlers for a compact footprint. DAF is highly suitable for eliminating fatty or oily compounds in wastewater which usually originate from industrial discharge (e.g. food processing, slaughterhouse). For municipal wastewater, DAF can be used for enhanced carbon extraction as primary treatment step in a WWTP, especially if industrial contribution with floatable organics is substantial.
- DAF technology of Veolia
- KWI Group: supplier of DAF Technology
- WPL: Supplier of DAF Technology
- Nijhuis Industries: Supplier of DAF Technology
- Veolia DAF process
- Suez flotation process
- Clarifying Treatment: Dissolved Air Flotation Provides Alternative for Treating Raw Water with Light Particles
-
Purpose
-
Approach
-
Where?
Microscreen (Drum+Discfilter)
Microscreen technology (drum- or disc-filter) employs woven cloth filter elements installed on the periphery of a drum or disc structure, and utilises an inside-out flow pattern. The filter works by gravity with a few cm of water pressure gradient and is robustly designed with few moving parts to ensure long life and low maintenance costs.
Water to be treated flows by gravity into the filter via the centre drum. The media mounted on the partially-submerged drum separates solids from the water. The filtered water flows through the media into the collection tank. Once solids have accumulated on the filter and a critical head loss is achieved, the media is cleaned by a counter-current backwash system. The filters are in continuous operation even during backwash and high solids events.
Coagulants and flocculants can be added upstream the filter unit in order to improve the filterability of the particles. The dose and type of chemicals applied also have an impact on the pollutant removal efficiencies that can be achieved in the microscreens. Such a feature allows for precise particle removal up to the values required by the user by careful control of the chemical dose (mg-chemical added/TSS to be removed).
- Hydrotech microscreen
- Film on Hydrotech drum filter technology
- Film on Hydrotech disc filter technology
Two-stage activated sludge
The 2-stage treatment concept for municipal WWTPs provides energetic advantages in term of reducing energy demand for aeration and enhancing the energy gain from biogas utilisation in CHP. The concept relies on a high COD-loaded activated sludge tank in the 1st stage where a higher percentage of COD - as compared to single-stage WWTP - is extracted from the wastewater stream with the surplus sludge.
In the 2nd stage which is operated at higher sludge age, nitrification and denitrification take place. Nitrogen removal can be optimised and adjusted to varying operating conditions by bypassing a part of influent wastewater in the 2nd stage for increasing the COD availability for denitrification or by returning a part of the nitrate rich WWTP effluent back to the anoxic zone of the 1st stage. The advantages of 2-stage treatment concepts could be confirmed at several large size WWTPs.
The energetic advantage of the 2-stage treatment configuration can be further increased by integrating a nitritation process to treat the ammonium-rich sludge dewatering effluent in sidestream. The treated wastewater stream can be then reintroduced in the 1st stage, promoting denitritation of the produced nitrite instead of denitrification. The saved COD load is then available for enhanced biogas production in the digester or for improving TN removal at plants with unfavourable TN/COD influent composition. In addition, the implementation of sidestream nitritation decreases operating costs of a 2 stage WWTP due to the better conditions for ammonium oxidation in sidestream than in mainstream (higher oxygen transfer rate).
Whereas sidestream nitritation combined with denitritation in mainstream is nearly energetically equivalent to sidestream anammox (oxygen demand in both cases ~ 1.5 gO2/gNremoved), nitritation exhibits a much more stable operation and lower investment and operation costs for process control.